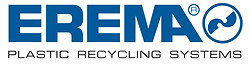
EREMA is the world’s leading manufacturer of plastics recycling machines and system components with more than 6500 installations of their systems in operation around the globe.
EREMA was founded in 1983 and is renowned for developing ever-improving, high-performing and environmentally friendly technologies for plastics recycling. EREMA’s technologies cover almost all areas from industrial plastics waste, post-consumer plastics waste to food-grade plastics recycling. Customers always enjoy the expertise and tailor-made solutions.
PET RECYCLING WITH VACUREMA AND VACUNITE
Since its launch in 1998, VACUREMA has become the world's most used system for PET bottle-to-bottle recycling. The core of the technology is the decontamination for food-grade in the flake form under vacuum, before extrusion. This leads to safer products, lower energy demand and higher product qualities. VACUNITE is the latest innovative system. It combines the proven VACUREMA system with the V-LeaN Solid State Polycondensation from Polymetrix. In this new system, all thermal process steps take place in nitrogen and/or vacuum atmosphere. Further, the benefits of the decontamination in flake form are combined with the flexibility for residence time in the Solid State Reactors at lower Vacuum requirements. This results in the highest decontamination efficiency, best colour values, top IV stability, and low energy consumption.The outcome: rPET pellets that exceed current legal requirements in terms of food-contact compliance. VACUNITE is the successful answer to increasingly stringent quality criteria for PET recycling to be approved for food contact.
EREMA – Market-Leader in Plastics Recycling
HDPE RECYCLING WITH A COMBINATION OF SYSTEMS
EREMA is the first machine builder to receive approval from the US Food and Drug Administration in 2019 for the post-consumer high-density polyethylene (PCR-HDPE) produced with the EREMA technology.
This technology includes three systems:
-
INTAREMA TVEplus
-
RegrindPro
-
ReFresher module
In combination, these systems produce the highest possible quality recyclate which allows food packaging to be made with up to 100% of this PCR-HDPE recyclate.
RECYCLING DIFFICULT MATERIAL WITH TVEplus AND RegrindPro
The extruder system INTAREMA TVEplus is a versatile machine for the most challenging task in post-consumer recycling: Recycling materials that are difficult to process such as heavily printed films and/or very moist materials. This is made possible by ultrafine filtration, thorough melt homogenisation and high-performance degassing. All in one step.The INTAREMA RegrindPro produces high-grade recycled pellets from thick-walled regrind by gentle processing and high-performance filtration. This is a versatile machine which can process a wide range of materials like PE, PP, ABS, PS, and other regrind types.
FIGHT HIGHER LEVEL CONTAMINATION WITH LASERFILTER
While conventional mesh screens can only handle up to 0.2%, the EREMA Laserfilter can process higher degrees of contamination of up to 5%. The key to success: short dwell times, static screens and a high-precision scraper that rotates only in the area of the still contaminated melt while maintaining constant pressure.The most outstanding part of the Laserfilter is its screen. With thousands of ultrafine drilled holes, it allows for filtration fineness of up to 70 µm. The permanent screen cleaning that takes place during the filtration process then quickly frees these holes to achieve high throughput rates even with heavily contaminated melt.

REMOVE ODOUR WITH THE ReFresher
The ReFresher is a high-efficiency anti-odour technology that allows for efficient post-consumer recycling. In combination with the INTAREMA TVEplus system, the ReFresher produces odour-optimised recycled pellets directly from contaminated post-consumer material. These odour-optimised pellets have a higher value and open new sales markets for recyclates from production and industrial waste.

EREMA INTAREMA® TVEplus® recycling machine with Refresher
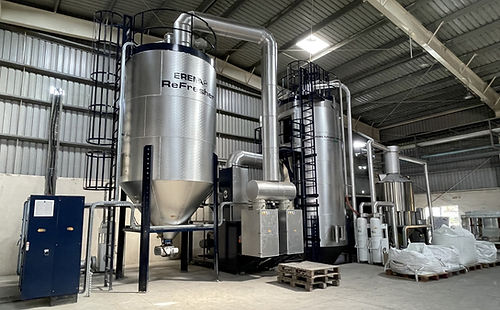
Banyan Nation (India), has combined its EREMA INTAREMA® TVEplus® recycling machine, on which the HDPE and PP waste is recycled, with a ReFresher to deodorise for food grade contact pellets.
A typical problem of household waste: it develops intense odours. These are caused not only by contaminants adhering to the surface but also by so-called migrated odour substances. The latter are caused by the packaging absorbing the odour of the food, cosmetics or cleaning agents inside it. The substances which migrate like this into the plastic are particularly stubborn.
Removing the entire spectrum of odours again as effectively as possible requires the support of the entire recycling process chain. This includes sorting and washing, plus the mechanical recycling process. Thanks to the effective interplay of the INTAREMA® TVEplus® with the innovative ReFresher technology it is possible to effectively eliminate a considerable amount of these odour substances again. While the TVEplus® extruder system primarily takes care of the high volatile, low molecular substances, the ReFresher also removes the low volatile, high molecular odour matter.
Thermal-physical cleaning process – without additives
The ReFresher technology keeps the pellets at the required temperature at which volatile materials can be discharged quickly and in depth. Particularly energy-saving: the ReFresher uses the system‘s own energy
from the pellets which are preheated through the extrusion process. Thanks to the ideal, stable process preparation in the INTAREMA® TVEplus® only relatively short residence times are required inside the ReFresher.
ReFresher:
-
Continuous odour discharge with hot flush gas
-
No complex vacuum system required
-
First in, first out: same treatment for all pellets
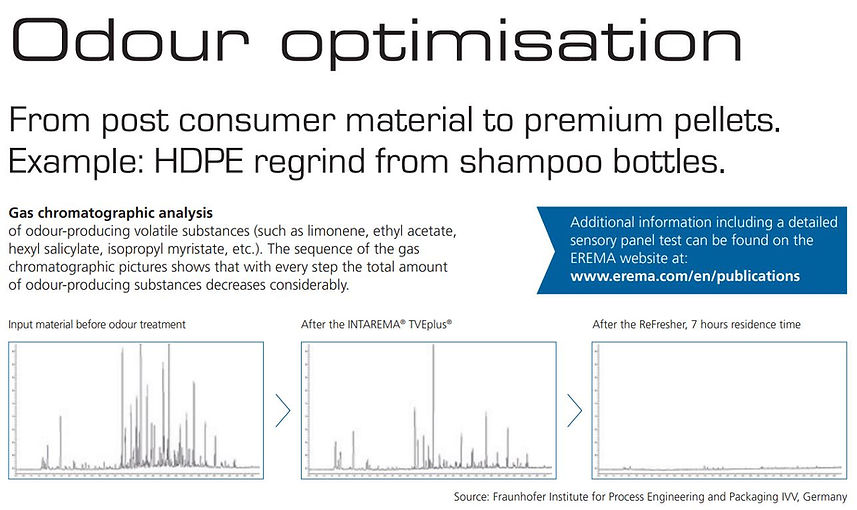
SUCCESSFUL FILM RECYCLING WITH ZeroWastePro
The new INTAREMA ZeroWastePro is a highly efficient recycling machine for in-house production-related film waste - specially designed for PE and PP films. The ZeroWastePro is suitable for inline as well as off-line application. The characteristics are the stability of the process, consistently high quality of the produced recycled pellets, and a high degree of automation.