Plastics Repelletising & Extruding
ALPHA by PLASMAC
​
PLASMAC’s ALPHA recycling extruder uses a unique Short Screw Technology (SST), which is based around a dual diameter 8:1 L/D ratio screw. The waste material is directly fed on to the screw meaning no prior size reduction is required, due to this little or no dust is produced which means a higher quality pellet is produced with the lowest levels of gels possible. The SST ensures low shear, runs at low melt temperatures and therefore guarantees an absolute minimum of material degradation.
With the minimal power consumption & the highest output / kW of installed power in the market, the ALPHA is giving lower running cost and therefore the quickest return on investment.
Further the ALPHA is the smallest footprint recycling machine available on the market.

OMEGA by PLASMAC
​
The larger OMEGA range features the unique direct shredding-extrusion combination. The waste material is fed in to the slow rotating shredder.
The unique screen design ensures minimal heat and dust resulting in higher quality pellet with the lowest levels of gels possible.
Combined with the low shear, low melt temperatures, the OMEGA guarantees an absolute minimum of material degradation.
​
The slow rotating shredder technology and unique screen design requires no cooling water of the rotor or transfer system to the extruder and hence reduces maintenance and costs.
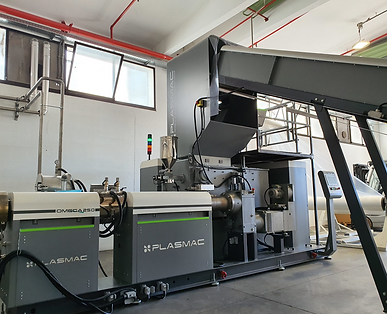
EREMA Decontaminate, Odour Removal & Extrusion
​
EREMA is the world’s leading manufacturer of plastics recycling machines and system components with more than 6500 installations of their systems in operation around the globe.
​
EREMA was founded in 1983 and is renowned for developing ever-improving, high-performing and environmentally friendly technologies for plastics recycling. EREMA’s technologies cover almost all areas from industrial plastics waste, post-consumer plastics waste to food-grade plastics recycling.
​
Vacurema by EREMA

Starting with highly efficient batch decontamination of the PET flakes. The patented pretreatment at elevated temperatures and under vacuum before the extrusion process removes moisture and migration materials from the feedstock very effectively and in a stable process environment. This prevents any hydrolytic and oxidative decomposition of the melt in the extruder.
​
Followed by an IV increase to the required level and then melting under vacuum.
The very short extruder screw without additional extruder degassing reduces the thermal stress on the material through minimised dwell time.
The robust, fully automatic filter removes even the smallest of aluminium, steel and other particles from the melt. The very large active filter areas enable filtration with up to 32 micrometers fineness at low pressure. The result is ultra-clean pellets.
The PET melt is cut in hot water and transported to the centrifuge, where the pellets are crystallised by latent heat crystallisation from the inside to the outside without the need for an external source of energy. The configuration and temperature control used for this process enable very high crystallisation rates (> 40%) without an additional post-crystallisation process. The advantage: fewer components, less consumption.
​
​

The combination with the patented, vacuum-assisted V-LeaN Solid State Polycondensation (SSP) and flushing with high-purity nitrogen increases the quality of the rPET pellets still further and ensures its compliance for food contact.
​
VACUNITE® is based on SafeFlake technology. As with VACUREMA® , extremely effective decontamination of the flakes in the vacuum reactor is the very first stage of the recycling process. This speeds up the process enormously.
​
Compared to pellets, flakes of the same volume have a larger surface area. For this reason, they dry much faster – and are already clean and dry when they reach the extruder. This creates an excellent basis for high-quality results.
​
A standout feature of VACUNITE® is the integrated nitrogen flushing during decontamination in the vacuum reactor. For this, nitrogen (N2) is used.
Unwanted yellowing is all but absent from the subsequent recycled pellets. Flushing significantly reduces the residual oxygen responsible for yellowing still further.
​
Energy accounts for a third of the costs of bottle-to-bottle recycling. With VACUNITE® , energy consumption drops by 36%. In combination, two innovative technologies become one uniquely effective system.
What makes VACUREMA® so remarkable is taken even further by VACUNITE® . Ultimate cleanliness, uniform IV values and perfect colour properties.
​
​
INTAREMA TVEplus by EREMA
​


With the INTAREMA TVEplus and ReFresher it is possible to recycle;
HDPE Bottle Flakes
HDPE Regrind Material
LDPE washed flakes, agricultural film
PE film with paper labels, pallet wrap
PE washed film flakes
PP film/non-woven fleece with solid content
Regrind material (PE, PP, ABS, PS etc.)​
​
The large-volume preconditioning unit ensures a long material residence time at high temperatures. In combination with Air Flush technology – which flushes the plastic with a continuous, hot stream of air – and the accompanying degassing, this results in elimination of the highly volatile odour substances prior to extrusion. And an additional bonus: high residual moisture in the material vaporises.
​
The reverse degassing and final double venting degassing zone at the extruder are particularly effective and remove any gas inclusions which are still present from the melt. One secret of the tremendous effectiveness here is the homogenisation zone which is located downstream of the filter and upstream of the final degassing and brings the melt to the temperature required for the end product.
​
Gentle melting and a short extruder up to filtration – what is good for the melt quality is also effective against additional odour development. This is because the gentle treatment at a low melt temperature and low shear forces means that impurities such as cellulose (wood, paper), rubber or silicone firstly do not burn and secondly are scarcely reduced in size. They remain large enough to be easily removed by the Laserfilter – before they can form unpleasant odours.
​
Output stage 1: Quality pellets
Perfectly filtered, homogenised and degassed – ideal for a multitude of high-end applications.
An additional bonus when using the continuous quality monitoring system
QualityOn: only exactly specified pellets enter the ReFresher.
ReFresher by EREMA
Contaminated post-consumer waste usually exudes intensive smells. However, EREMA has a technology that enables removal of even migrated odours during recycling. The innovative ReFresher (stage 2) in combination with the INTAREMA® TVEplus® (stage 1) prove to be a highly efficient double act.
​
The ReFresher cleaning process eliminates odours caused by low volatile, high-molecular substances. The technology keeps the pellets at the temperature required for fast and deep-cleansing discharge of volatile materials. Particularly energy-saving: the ReFresher uses the system's own energy from the pellets which are preheated through the extrusion process. Thanks to the ideal, stable process preparation in the INTAREMA® TVEplus® only relatively short residence times are required inside the ReFresher.

INTAREMA FibrePro: IV by EREMA
​
When it comes to PET fibres, EREMA offers the INTAREMA® FibrePro:IV. Ready for respinning, the 100% rPET pellets produced have high colour fidelity and the excellent mechanical properties needed for further processing into ultra-fine, 100% recycled PET fibres suitable for filament, staple and BCF fibres.
​
As a result of its efficient cleaning and recovery performance, the new INTAREMA® FibrePro:IV is also the first choice for especially challenging input materials such as PET fibres that are heavily contaminated with spin finish and have high levels of moisture.
​
This is made possible by combining the INTAREMA® machine, which has proven itself thousands of times over, with innovative IV Uptimiser technology. While the INTAREMA® prepares the material for extrusion using its Preconditioning Unit and Counter Current technology to ensure perfect homogenisation, pre-drying, removal of volatile components, and subsequent gentle PET melting, the new IV Uptimiser ensures repolymerisation, IV lift and efficiently cleans the fibres of finishing additives.
​
EREMA is leading the way in PET fibre-to-fibre recycling with innovative solutions - an important contribution to today's circular economy.

