Westeria’s AirLift windsifter system delivers what it promises
- cemac
- May 28, 2021
- 2 min read
Updated: May 2, 2023
As is always the case, biowaste suffers from impurities when citizens also throw plastic, glass, and metal into their organic waste bins. The recipients of compost made from treated biowaste, primarily the agricultural and gardening industries, must be able to mix sorted compost – without impurities – into the earth.

This means complex new technologies are required for treating biowaste to make compost, and that is why the city of Lübeck, Germany, decided upon Westeria’s AirLift windsifter system. Thanks to this technology, the compost quality is excellent, meeting not just customer expectations, but also the requirements of the Federal Compost Quality Association.
“With the use of Westeria’s AirLift system, we achieve a compost quality that is considerably below the permitted number of impurities such as plastic film, and therefore rate the new standard of compost extremely positively,” says Manfred Rehberg and Roman Gradert, heads of the city’s cleansing department and biomass plant.

Lübeck city installed a windsifter manufactured by Westeria, with its accompanying SpeedCon high-speed conveyor belt plus AirWheel module, to meets the city’s requirements. Materials such as plastic, which have a similar specific density, must be reliably separated, and Westeria’s windsifter achieves a degree of purity of over 99 %.
At a speed of up to 4 m/s, the material is flung over a bend in the conveyor belt as the AirLift positioned above sucks up any lightweight material. The heavier bits of biowaste remain on the sloping belt. At the same time, the patented belt steering system prevents the belt from moving in the guide, meaning these belts have a longer service life.
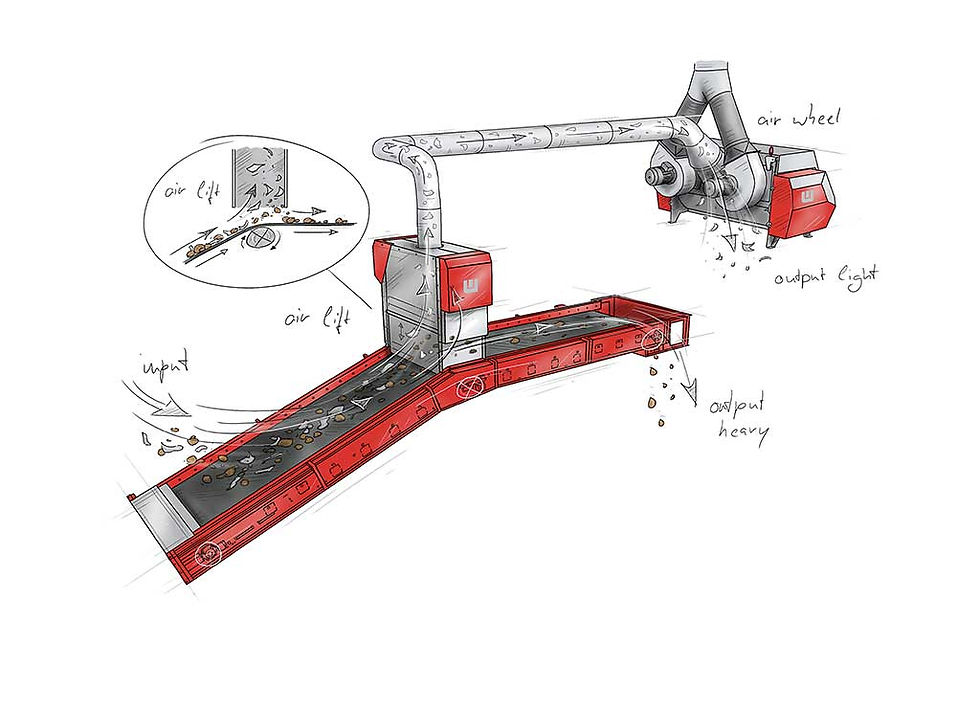
The fact that the AirLift can be precisely adjusted in terms of air volume and air speed, results in extremely efficient ballistic trajectories, guaranteeing that a high yield of impurities can be separated.
In Lübeck, this occurs with a conveying capacity of 30 tonnes/hour and an impurity grain size of up to 20 mm. The technology deployed by Westeria can achieve throughput of up to 320 m³/h, depending on the material.

The lightweight materials sucked up in this way travel through a pipe system to the subsequent treatment stage AirWheel. This uses a rotating drum screen to ensure that fine compost materials are separated off. These are then mixed back into the finished compost as valuable constituents.
The special seal system that is fitted prevents material components entering yet allows fine materials and water to penetrate unimpeded.

The system’s ease of maintenance is underscored by the AirJet cleaning system, which feeds in compressed air, and the lever mechanisms and switching elements which are all accessible from outside, enabling inspections to occur during operation. Likewise, the anti-blockage system, which automatically raises the AirLift’s infeed gate to prevent blockages caused by build-ups of material.
“We are delighted by the results achieved by the windsifter technology we have in use. If, with a throughput of 250 tonnes of compost, you can see the yield of 250 kg of formable plastics ˃2 mm with your own eyes, then the new purity level that our compost achieves, with only 0–10 cm2/l of remaining impurities, can only be emphasised,” explains Roman Gradert with satisfaction.
“As a result, we are also in a good position for bringing our compost onto the market in future.”
_____
CEMAC technologies represents WESTERIA in Australia.
CEMAC technologies
03 8400 6066
Comments